电池箱安装点静刚度分析
电池箱是一种用于存放电池组的容器,主要对电池起支撑和保护作用。近几年,新能源汽车越来越普及,随之而来的问题是当内置的电池组发生碰撞后易起火甚至爆炸,严重危害车内乘客的生命财产安全。电池箱是保护电池组安全性的重要结构。电池箱的刚度和强度,直接关系到电池组受碰撞程度,从而影响新能源汽车的整体安全性。本案例使用Simhub结构静力分析模块对电池箱安装点的静刚度进行仿真分析,以确保电池组在行车过程中的安全性,并为电池箱结构的进一步优化设计提供数据支撑。
电池箱物理性质¶
电池箱主体结构由上盖和下盖组成,用合适的方式将二者连接,以维持箱体的稳定从而保护内部电池。电池箱对电池组的保护作用体现在以下几个方面,如:帮助电池通风散热、使电池绝缘与防水、保护电池免受撞碰等。本案例主要讨论电池箱是如何保护电池免受碰撞的。
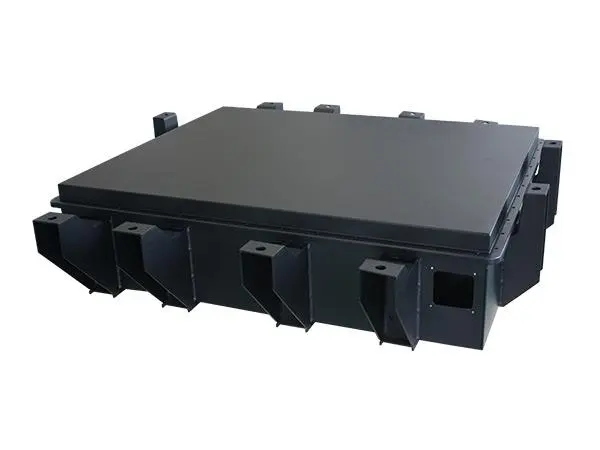
为了使电池免受碰撞,需要减小箱体受冲击时的变形,以防挤压内部电池从而导致电池起火。因此,测试箱体在冲击载荷下的刚度十分重要。这里我们将冲击载荷等效为静载荷,通过测试电池箱的静刚度,以检验电池箱在遇到突发情况下的安全性。
在仿真过程中,我们主要分析电池箱在设计载荷作用下的变形大小。设计要求电池箱各安装点的z向刚度Kz≥2000N/mm。
建模仿真流程¶
电池箱的静刚度测试可以视为结构静力分析问题,因此选择Simhub里面的结构静力分析模块进行仿真测试。
模型导入¶
Simhub平台为简化仿真流程,暂不支持几何建模功能。因此,本案例使用客户提供的STEP格式几何模型,导入Simhub的结构静力分析模块进行仿真。
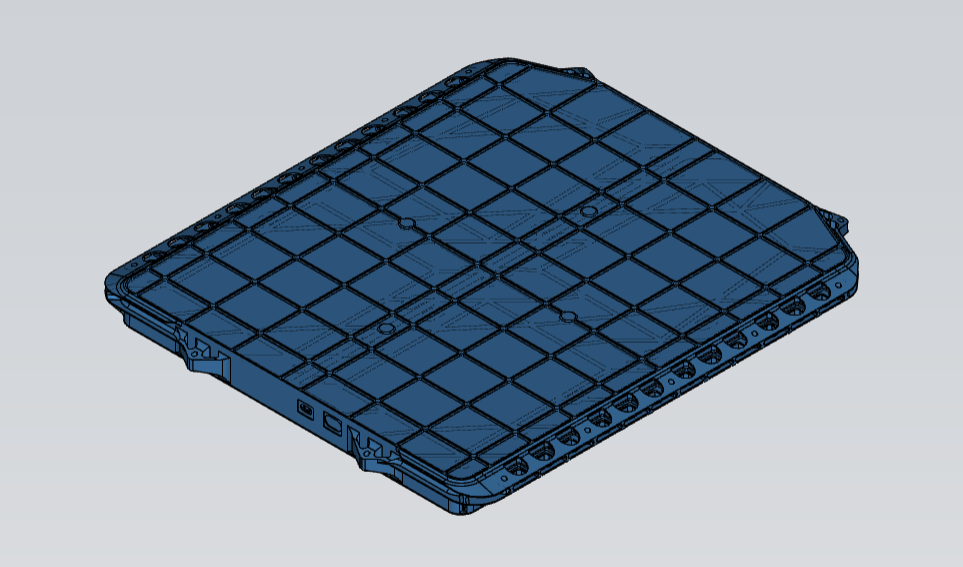
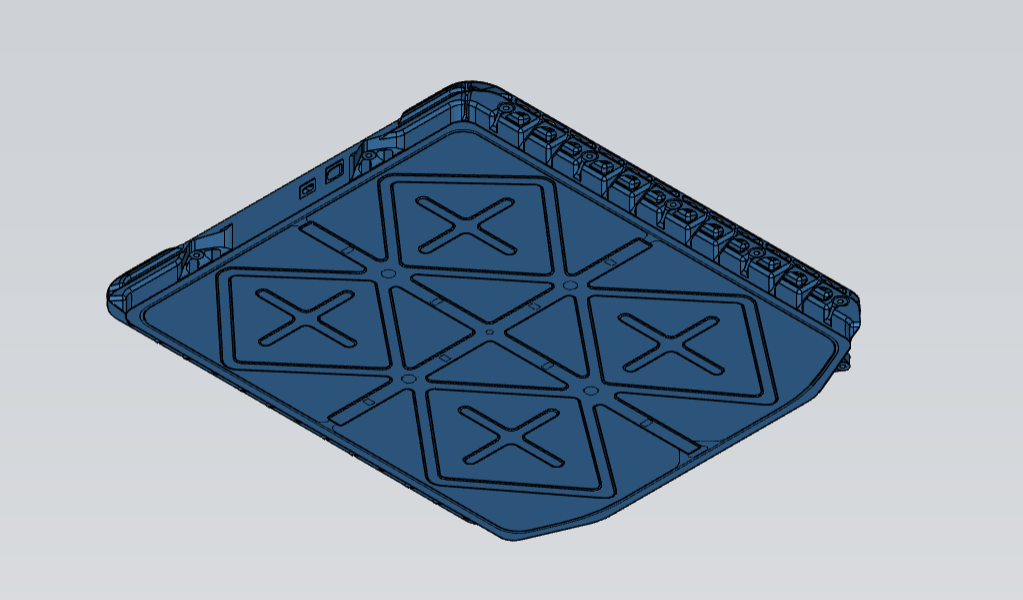
材料性能¶
材料性能对于计算结果的准确性至关重要。本案例中,电池箱的制造材料为ZL114铝合金,其材料参数如下表所示:
材料 | 密度(kg/m3) | 弹性模量(GPa) | 泊松比 | 屈服强度(MPa) | 抗拉强度(MPa) |
---|---|---|---|---|---|
ZL114 | 2680 | 70 | 0.33 | 230 | 290 |
网格设置¶
因为电池箱模型几何复杂,在保证数值收敛性的同时为减少运算时间,在网格设置中将二阶单元改为一阶。
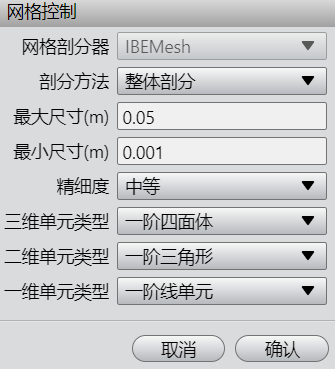
边界条件¶
电池箱通过螺栓连接上下箱体,在本案例中可将其简化为固定连接。根据模型简化,在一个安装点上施加1000N的集中力;同时在其他安装点上施加固定约束。
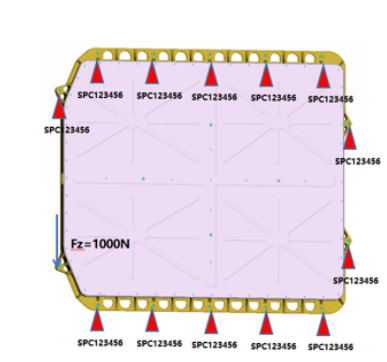
结果研究¶
为了研究电池箱的静刚度,在给定集中力载荷的情况下需要查看结构的变形大小。在计算完成后,右键点击模型下方的子节点可以切换至位移结果。
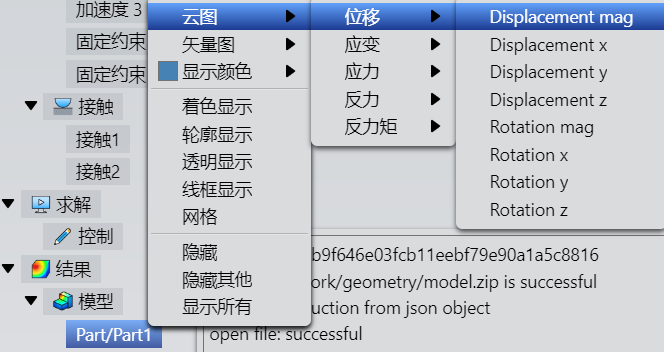
通过查看位移结果可以发现,在1000N的集中力载荷下最大位移约为0.1mm。相较于宽度为0.1m的电池箱而言,该变形量仅为结构尺寸的0.1%,不会影响内部电池组的安全性。此时电池箱的z方向静刚度:Kz=1000/0.07282N/mm=13732.49N/mm。 若要放大查看结构的变形,可在上方结果设置里调整合适的缩放系数。
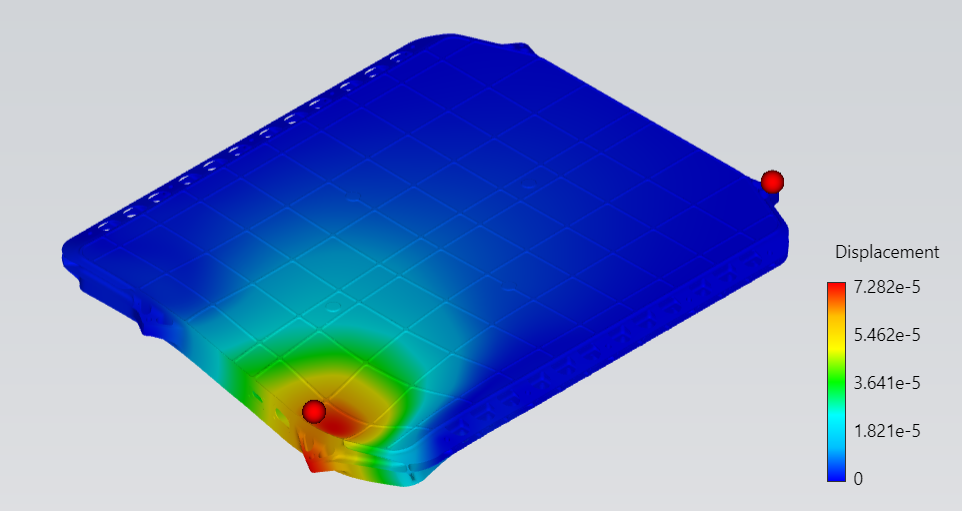
观察切面图可见,由于电池箱内部是中空结构,在集中力载荷作用下易发生变形。由此分析可知,增加电池箱的刚度可采用以下2种方式: 1、增加上下表面厚度; 2、在电池箱内部布置加筋梁。
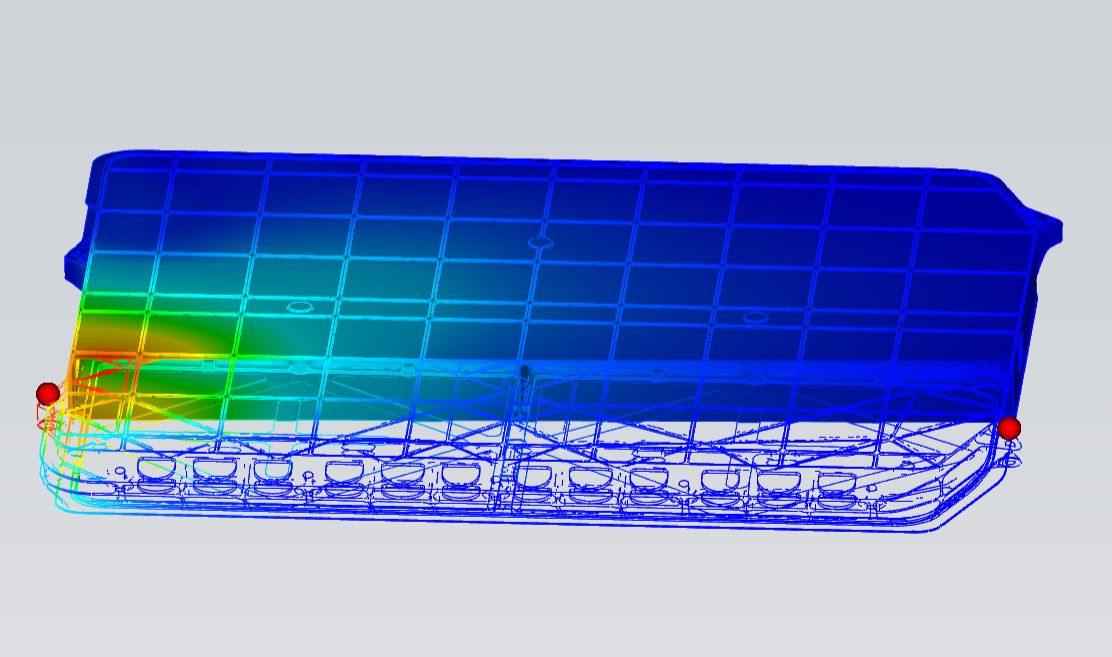
为了测试不同部位的静刚度,选择多个不同位置的安装点进行仿真。
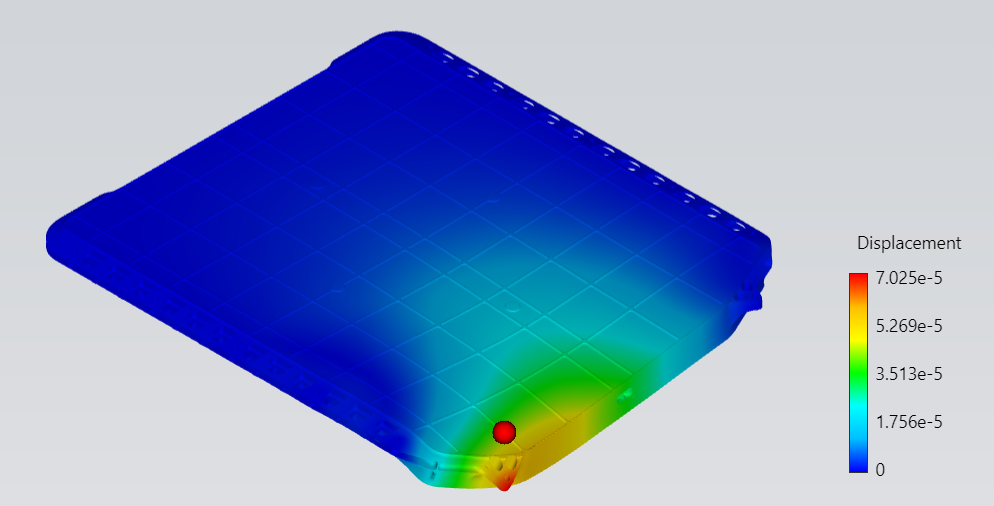
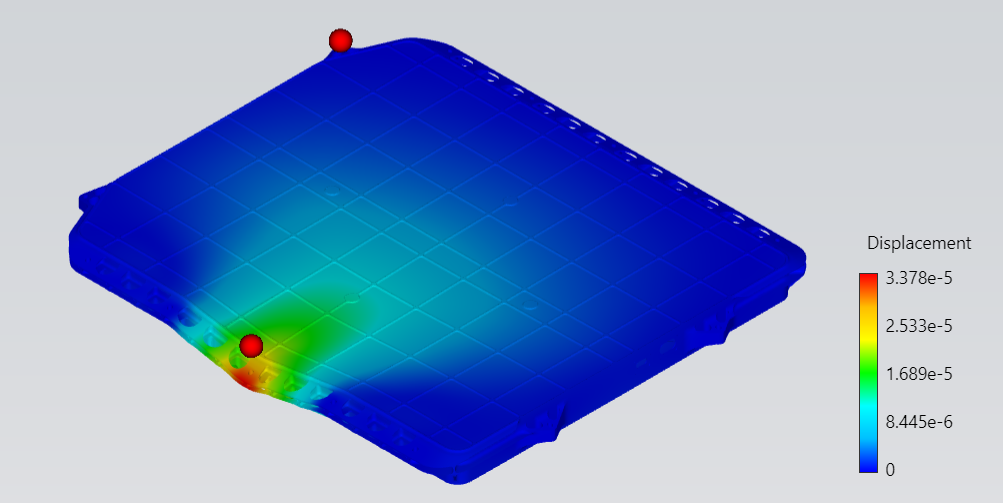
观察各安装点的结果,发现最大位移分别为7.025x10-2mm和3.378x10-2mm。由此可见,电池箱各安装点的z方向静刚度均不小于13929.52N/mm,整体满足kz≥2000N/mm的设计要求。
结语¶
本案例介绍了如何利用Simhub的结构静力分析模块研究电池箱的静刚度问题。Simhub结构分析模块还支持许多其他分析类型,功能涵盖结构模态、预应力模态、谐响应及瞬态动力学分析等,欢迎大家探索和使用,并给我们的软件提出宝贵的改进意见。
下面是相关工程文件。模型复杂,如遇卡顿还请耐心等待。
https://dev.lan.iadiae.com/app/gallery/main.html?uuid=Gd3-Q2JRMyrkrXzzPaLqBZXu